Chapter 4. Exotic Processes and Materials
There are a few rather unique approaches to 3D printing that are substantially different from the broad categories already outlined, or different enough that they deserve their own consideration independent of the more popular methods. These 3D printing processes often have a single manufacturer or are otherwise not widely represented in comparison to previously described methods.
Laser Engineered Net Shaping (LENS)
Created by Optomec, the LENS process operates by spraying particles (typically ~100 microns in diameter) into a melt pool created by a laser beam. It is an extension of the laser cladding process, allowing a variety of materials to be deposited onto a surface that moves underneath the business end of the laser. While the process is primarily used to deposit metallic materials, deposition of glassy materials has also been demonstrated.
Figure 4-1 shows the LENS process in action.
While the LENS process can be used to build up components from scratch, much like the other 3D printing methods, it can also be used to deposit layers onto non-planar geometries. Thus, unlike most AM methods, the LENS approach is also useful for repairing extant components and not simply for the production of new parts.
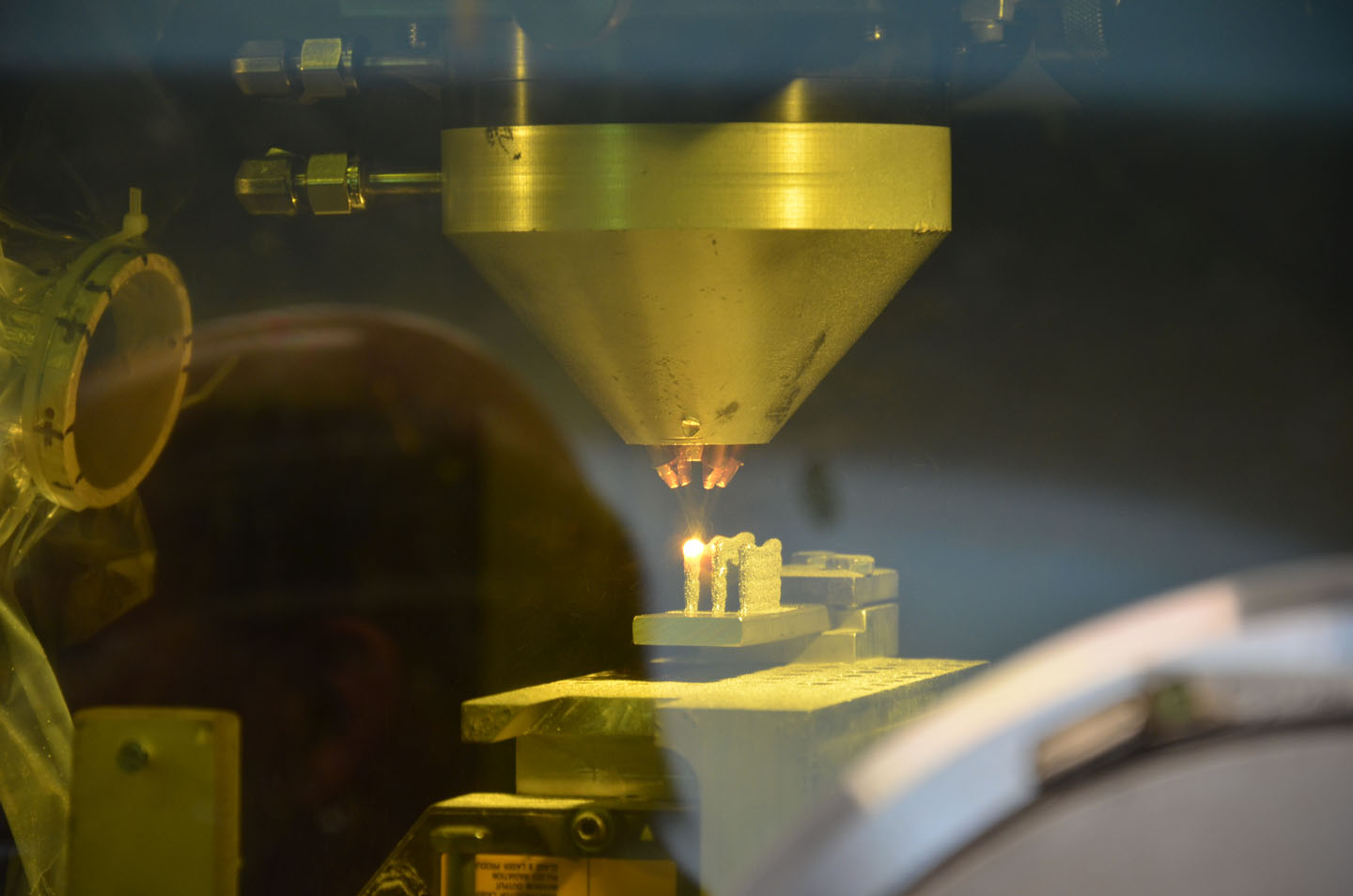
Figure 4-1. The LENS process in action, employed by researchers at Penn State University’s CIMP-3D facility
One of the more exciting possibilities of LENS is the grading of multiple materials, which can be obtained by changing the type of powder being sprayed into the melt pool. While a few AM processes allow the deposition of multiple materials, these materials typically have fairly abrupt interfaces. As many types of failure are caused by abrupt changes in material class, it is hoped that graded interfaces might create a more robust design in the future (assuming we can produce them!).
Laminated Object Manufacturing (LOM)
Laminated object manufacturing is one of the older approaches to 3D printing, which produces a type of composite object from individually laser-cut layers. In its most rough form, a series of paper parts are punched out and glued together by hand, with each piece representing a single layer of the final object. With a roll-to-roll process and a build region, it is possible to automate this procedure, which greatly speeds up the associated time and improves the accuracy of the final part. The final part is wood-like in behavior, assuming that paper was used for each layer.
The amount of waste created by throwing away unused paper is more similar to traditional subtractive methods, so perhaps LOM might be considered a sort of stepping stone between traditional methods and 3D printing.
Biomaterials and Bioprinting
Bioprinting is an exciting subject. Who doesn’t want to print themselves a replacement organ? Indeed, the plots of several dystopian films might be discarded entirely if we could do such things, but as is often the case with such ideas, it is easier to express than to perform, for both biological and technical reasons.
One technical issue lies in the creation of vasculature. Humans typically have both large veins/arteries and small capillaries. Building a printer that can create objects at one scale or another is not too difficult, but merging them into a system that can create features at both large and small scales is difficult.
There are some commercial offerings in the bioprinter area, but it is hard to determine what these systems are truly capable of, in comparison to the custom devices created by researchers. Organovo, for example, has been offering a system for some time that is supposed to be able to make miniature livers. Anyone interested in bioprinting would probably benefit from looking into tissue culture more generally.
There has been much discussion of food printing, which might be considered a class of bio-friendly printing materials. An ever-increasing number of 3D-based food production methods have been proposed and built, though most appear to be novelties for the time being. Whether or not this is an elaborate form of “playing with your food” remains up for debate.
Loaded Materials (Wood, Metal, Carbon Fiber)
Within the FFF space, a number of new and strange material choices are starting to become more common. Plastic filaments (the feedstock for the FFF process) can be loaded with wood particles, metal powder, or carbon fiber, creating a final print with properties somewhere between that of its constituent components. More and more users in the consumer space are beginning to experiment with these material options as new suppliers step forward.
The use of wood-impregnated filaments (sold as LayWood) has prompted some imaginative users to vary their extruder tip temperature during the printing process, changing the resulting color and finish of the printed part. The final result is even more wood-like than would otherwise be produced and represents an interesting development in the consumer space.
Get 3D Printing Primer now with the O’Reilly learning platform.
O’Reilly members experience books, live events, courses curated by job role, and more from O’Reilly and nearly 200 top publishers.