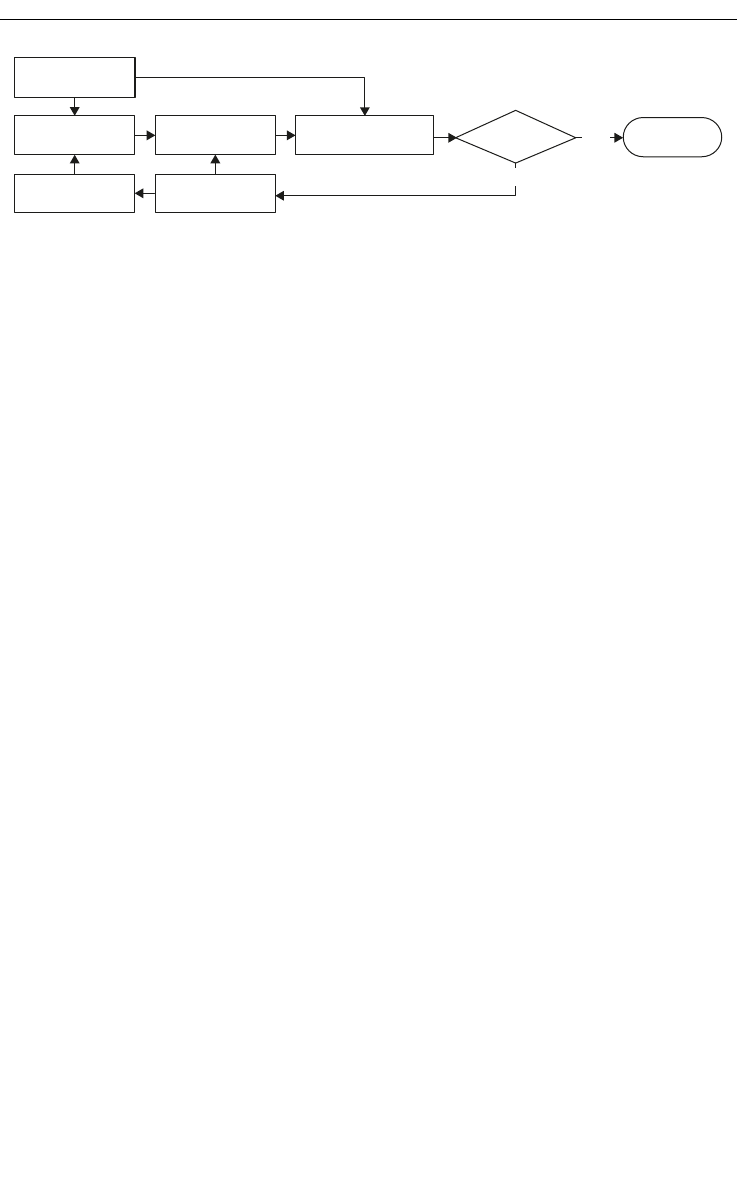
However, one can control results by installing sensors before, during or after the results
are created. It all depends on where you install the sensor, what you measure and the
consequences of failure.
The progressive development of controls from having no control of quality to installing
controls at all key stages from the beginning to the end of the product cycle is illustrated
in Figure 1.5. As can be seen, if you have no controls, quality products are produced by
chance and not by design. The more controls you install the more certain you are of pro-
ducing products of consistent quality but more control does not mean more inspection.
Control before the event
Some failures cannot be allowed to occur and so must be prevented from happening
through rigorous planning and design. One example is the use of reliability prediction
performed before the design is complete to predict whether product reliability will meet
the specification. Another is the use of competence-based assessment techniques where
personnel are under close supervision until they demonstrate competences following
which supervisory controls are removed. This allows you to remove output checks because
you know that if you were to inspect the work you would find it to be correct. Instead
of checking every product produced, you check competency periodically and assign
responsibility to personnel for checking their own work. Another method is the use of
prevention-based error-proofing mechanisms that sense an abnormality that is about to
happen, and then signal the occurrence or halt processing, depending on the severity,
frequency or downstream consequences.
Control during the event
Some failures must be corrected immediately using automatic controls or error proofing.
By continuous monitoring of parameters in a processing plant the temperature, pressure,
quantities, etc. are adjusted to maintain output within specified limits. Electronic compon-
ents are designed so that they can only be inserted in the correct orientation. Computer
programs are designed so that routines will not run unless the correct type of data is
entered in every field.
Basic concepts 31
Requirement
Plan Do Check
Remedial
action
Corrective
action
Conforms?
No
Feedback loop
Product/
service
Yes
Figure 1.4 Generic control model
H6663-Ch01.qxd 6/29/05 9:57 AM Page 31
Get Automotive Quality Systems Handbook, 2nd Edition now with the O’Reilly learning platform.
O’Reilly members experience books, live events, courses curated by job role, and more from O’Reilly and nearly 200 top publishers.