13
Application – Design of a Composite Panel
Perhaps the best way to see how the concepts and methods presented in previous chapters can be used is through a typical application. This provides insight into how the geometry and layup for different components can be selected avoiding failure in any of the expected failure modes while maintaining competitive weight and cost. A formal optimization for weight and/or cost is not done here. Instead, cost and weight trades among different designs will be performed to highlight the advantages and disadvantages of different concepts and to show how different decisions on design concept, geometry and layup affect the design outcome.
The application selected is a fuselage panel as shown in Figure 13.1.
Figure 13.1 Portion of fuselage to be designed
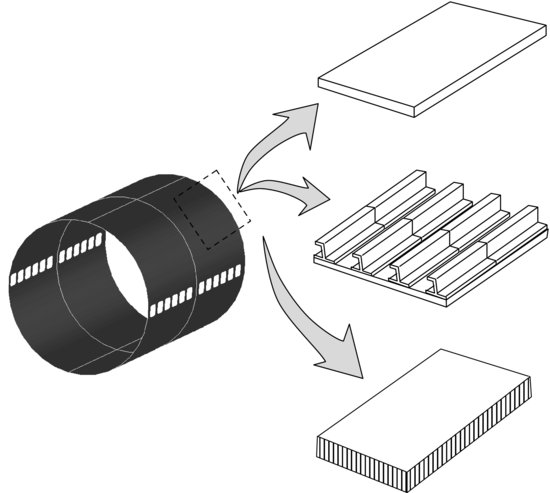
Two separate loading conditions are considered:
In addition, the out-of-plane deflection for the pressure load case must not exceed 2.0 mm. The panel dimensions are 1.5 m × 0.75 m. Three different design concepts, monolithic, stiffened and sandwich panel will be considered. The panel is attached to adjacent structure with fasteners. In all cases, for simplicity, the panel is assumed to be flat.
Table 13.1 Properties of candidate materials
Property | Unidirectional tape | Plain-weave fabric |
Ex (GPa) ... |
Get Design and Analysis of Composite Structures: With Applications to Aerospace Structures, 2nd Edition now with the O’Reilly learning platform.
O’Reilly members experience books, live events, courses curated by job role, and more from O’Reilly and nearly 200 top publishers.