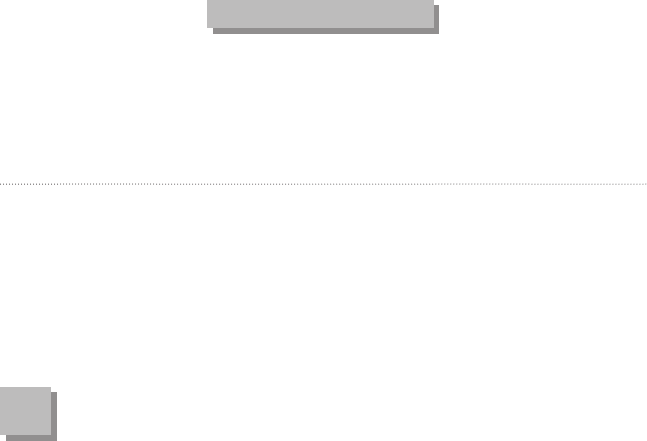
· 2 2 5 ·
T
his chapter is all about developing a capability to service cus-
tomers, at speed. However, to be in a position to react quickly
requires spare capacity located throughout the system, and this
comes at a price. So it may be necessary to select those customers
you want to deal with, and cull the rest. It’s a choice you have to
make because resources are not unlimited. To achieve speed also
requires breeding a subculture which will support fast decision-cycle
times, and here the OODA loop, borrowed from the military, comes
into play. To get the desired results it is necessary to configure your
organization for speed, and populate it with individuals who are
comfortable with working fast and prepared to take measured risks.
This is not a place for consensus-seeking individuals.
It is the third millennium. We all want to be better, cheaper and faster.
Let’s make that faster, faster and faster. Stop the planet, I want to
get off! A new breed of enterprises is certainly demonstrating what is
possible when it comes to responding to customers in a fast-moving oper-
ating environment, where life-cycles are short and variety reigns supreme.
Apparel companies Zara, Adidas and Staroup; technology companies
Dell, Nokia, Apple and Cisco; medical appliance manufacturer Cochlear;
and supply chain service company Li & Fung are among these leaders.
The winners in this environment are those that can respond urgently and
C H A P T E R 9
Agile supply chains
Where quick response is paramount
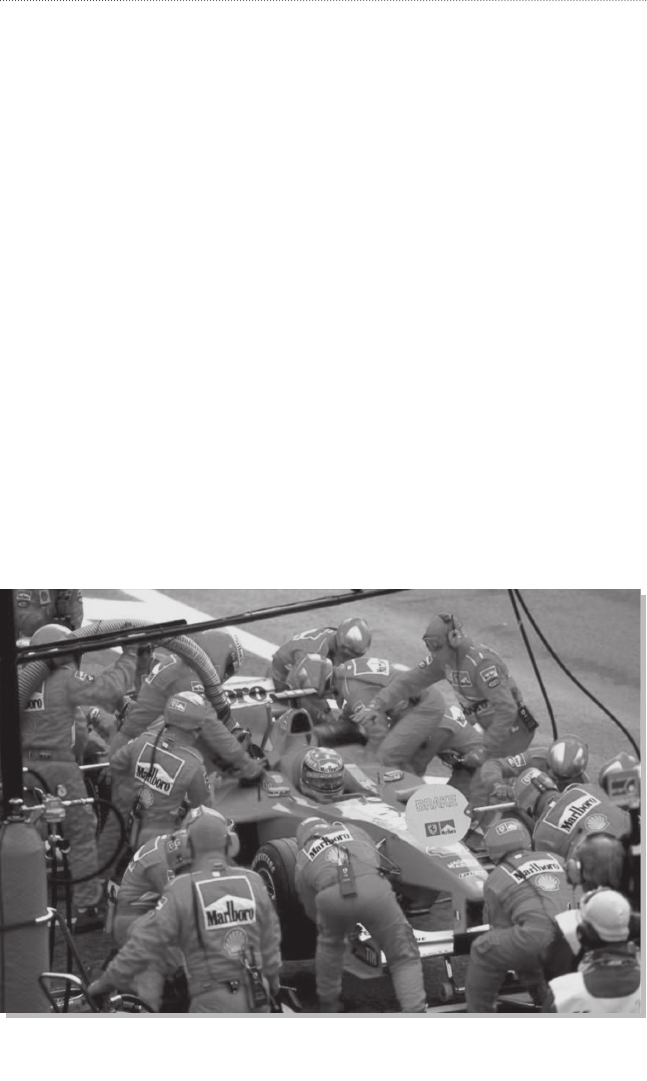
D Y N A M I C S U P P L Y C H A I N S
· 2 2 6 ·
effectively. Think of the ultimate example set by the pit crew during a pit
stop in a Formula One car race as depicted below. The highly skilled indi-
viduals in the crew work in perfectly executed harmony, racing against the
clock and doing so in a confined space. This is a world where millisec-
onds count, where we worry about speed of execution first and the spare
capacity required and the cost involved, a distant second. Races have
been won and lost during pit stops. But good planning also underpins a
quick response. Many pit stops are scheduled and therefore predictable
– planned to the lap. It’s the unplanned pit stops where you see the differ-
ence between success and failure, winners and losers.
The world for businesses operating in agile supply chains is similar; the
only thing is we have neither the budget nor the capacity of an F1 team
standing-by on alert 24/7, 365 days a year. Yes, speed is paramount in
this twenty-first-century world. But in keeping the roving, foraging cus-
tomer firmly in our sights, we need to deliver in a cost-effective way;
otherwise we will find ourselves careering off the track in a high-cost,
high-speed wreck. Possibly, we are getting a little carried away. But the
point is: is such an extreme response necessary for all our customers? As
PHOTO 9 .1
A Formula One pit stop
Source: © Schlegelmilch Photography
Get Dynamic Supply Chains, 2nd Edition now with the O’Reilly learning platform.
O’Reilly members experience books, live events, courses curated by job role, and more from O’Reilly and nearly 200 top publishers.