Robots-Provision
D107-99 / 4225
162
| FIRST Robots
FOUR-
WHEELED
SHOOTING
Team 1114 began the design process with a simple
question: Do we move or stand still? The question was
not about the robot’s overall action, but about its function
during shooting. This single question guided the robot
design and helped the team, from General Motors-St.
Catherine’s Powertrain & Governor Simcoe Secondary
School in Ontario, Canada, think about possible alternatives.
The team decided to use a fixed launcher on the robot to
keep the design and controls simple. A fixed launcher
required that the entire robot base be used as the aiming
mechanism, rather than using a turret to aim at the goal.
Recognizing that the robot would need to stay in one position
to shoot multiple balls, the team designed a drive train and
control sequence to ensure this condition. High traction, tank-
style treads were selected for propulsion, with the expectation
that the high levels of friction from the treads would also
resist motion from opposing robots.
A control algorithm was written to keep the robot station-
ary while shooting. Sensors monitored the original location
of the robot before shooting commenced, and a feedback
system kept the robot in position. Referred to by the team
as “drive base lock,” this condition freed the robot operators
from worrying about maintaining position in the often
congested area in front of the goal.
By analyzing the trajectory with ball projectile formulas,
including consideration of air resistance, the team calculated
the necessary tilt angle of the shooter. With a 29-degree
shooting angle, the robot could hit every shot at the upper
goal from distances between 7 and 27 feet (2.1 to 8.2 m).
As such, there was no need to further complicate the design
with an adjustable tilt mechanism. By keeping the shooter
angle physically fixed and the robot base dynamically fixed,
the team created a simple design that was further augmented
with effective control strategies.
STILL ON
TARGET
C
C
TEAM 1114
RF_162_179.qxd 2/1/07 10:31 AM Page 162
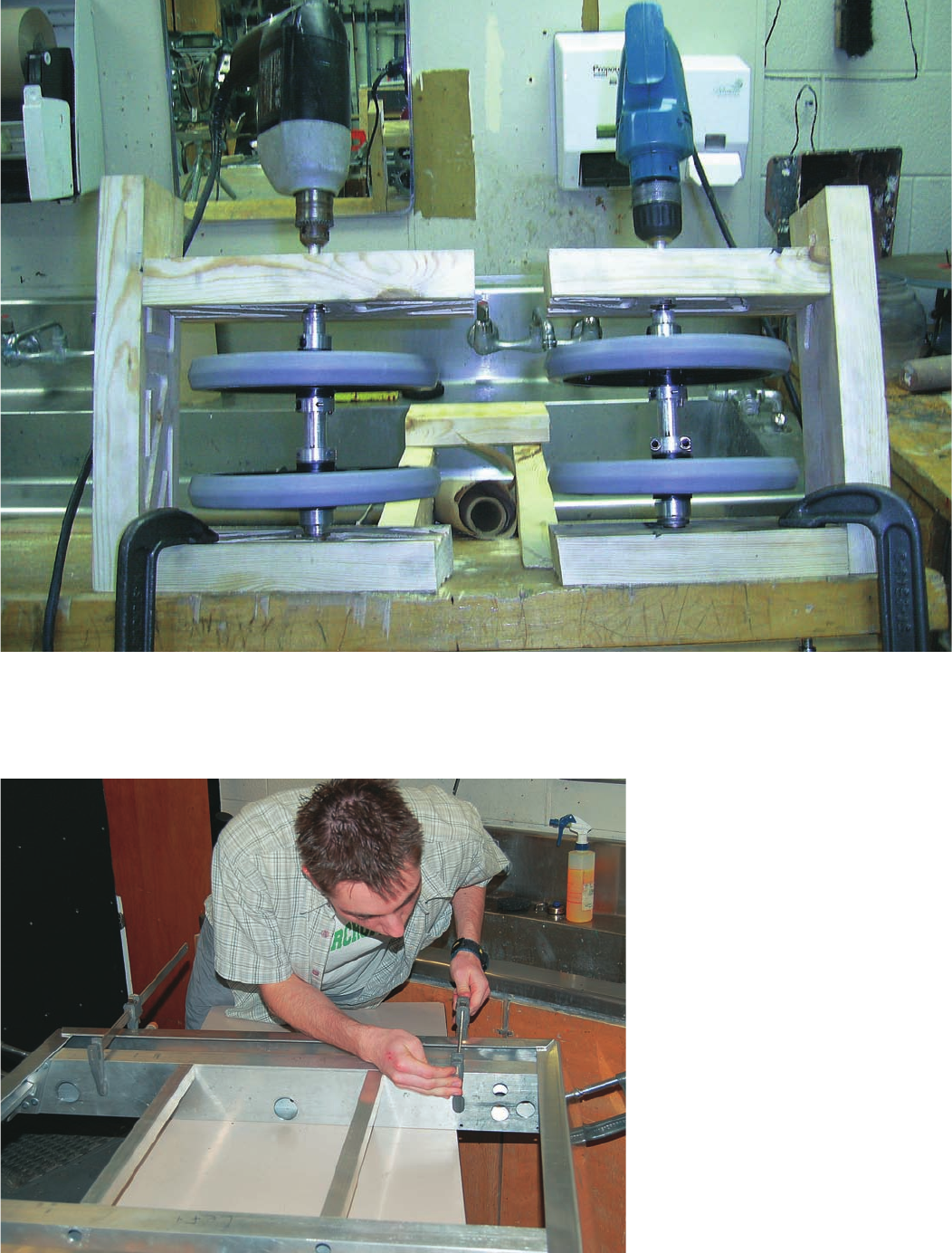
Robots-Provision
D107-99 / 4225
163
Innovation in Control Award
|
Early in the design process, Team 1114
investigated a four-wheel shooting system.
The system performed well.
Robot Creation
Team 1114 experimented with a
four-wheeled, wood-framed shooting
system at the beginning of the robot
design process. The design began with
an aluminum base, outfitted with four
drive motors and multiple speed trans-
missions, to provide a range of power
for different driving conditions. The
base was augmented with tread propul-
sion and a multiple-band ball pick-up
system. The shooting system, towering
over the base, was positioned at the
height needed to shoot over opposing
robots. A ball-storage hopper, con-
structed with polycarbonate panels on
a
PVC frame, completed the design.
The robot frame is constructed from
aluminum plate and bar stock, cut to length
and welded together. The design includes
foundations and supports to mount motors
and other robot systems.
C
C
C
C
C
C
RF_162_179.qxd 2/1/07 10:31 AM Page 163
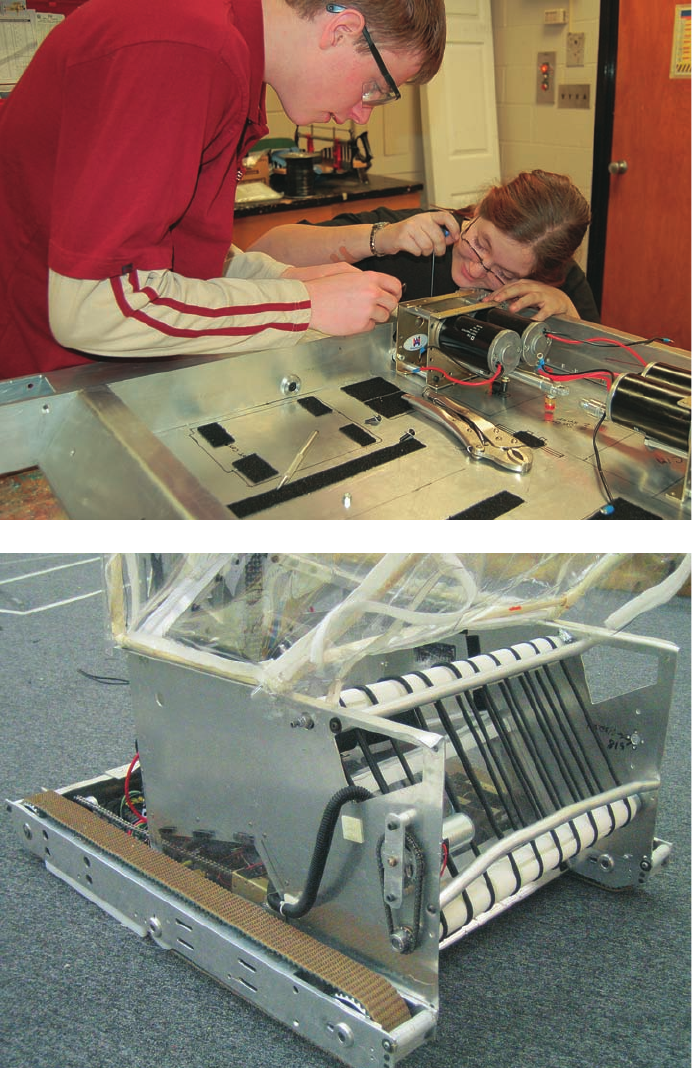
Robots-Provision
D107-99 / 4225
164
FIRST Robots
|
Each aspect of the robot was mod-
eled using computer-aided design soft-
ware. Even the operator control panel
was initially planned using computer-
based design tools before it was con-
structed with real dials and switches.
The computer-aided drawings served
as a record of the design that was eval-
uated to examine functions and make
improvements.
Control Features For
On-Target Shots
Intuitive control was a guiding principle
for Team
1114. This strategy, adopted
to simplify driving, led to the creation of
four control features: drive base lock,
autonomous target check, camera aim-
ing, and curved shooting.
Drive base lock was the control algo-
rithm developed to maintain the robot’s
position and orientation at a specific
location on the field. A simple click of
the joystick trigger relinquished driver
control to the onboard microprocessor.
Using wheel encoders and a gyrocom-
pass, the microprocessor detected any
motion and automatically corrected that
motion to maintain position. In this
mode of operation, the robot would
automatically fight to stay in position,
thereby creating a stationary platform
from which to fire balls into the goal.
Autonomous target check was
applied to continually monitor the cam-
era output for the presence of the target
light. If the robot was knocked off
course and the camera lost the target,
the ball firing mechanism halted and the
robot automatically turned back in the
direction of the light until the target was
relocated. This feature ensured that
balls would only be fired when they
could be scored.
C
C
The inside of the frame includes a tray to
support other robot systems. Dual motors on
each side of the robot, along with a gear box
capable of operating at different speeds, provide
the robot with a range of power.
Tread tracks drive the robot and keep the
center of the machine free to collect and lift balls.
C
C
C
C
RF_162_179.qxd 2/1/07 10:31 AM Page 164
Get FIRST Robots: Aim High now with the O’Reilly learning platform.
O’Reilly members experience books, live events, courses curated by job role, and more from O’Reilly and nearly 200 top publishers.