Chapter 2Holes
One of the most common stress risers in a composite structure is a hole. The presence of holes is inevitable in an airframe. Even though assembly methods other than fastening are used through increased co-curing and adhesive bonding, some fastener holes are always present. In addition, lightening holes (to reduce weight), holes to accommodate systems equipment (hydraulics, electrical, etc.) and window and access door cutouts are ever present (Figure 2.1). Finally, holes (punctures) created by tool drops, runway debris or other forms of damage also occur during service.
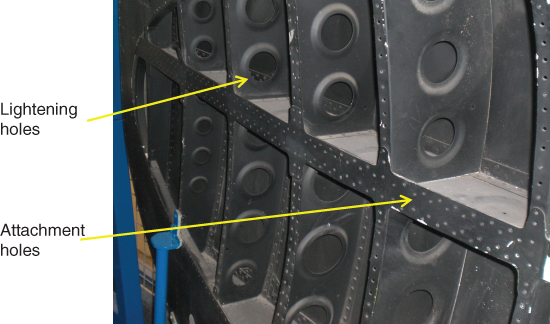
Figure 2.1 Fuselage structure with lightening and attachment holes
Knowing how a composite structure responds in the presence of holes is, therefore, very important for generating robust and damage-tolerant designs. There is one additional reason for understanding how the strength of a composite structure is affected by the presence of a hole: Holes can be used to model other more complex forms of damage. Treating impact damage or through-thickness cracks as holes of equivalent size can simplify the design and analysis of such structures.
There are different types of holes depending on their shape and whether they are loaded or not. In addition to circular holes which will be the focus of this chapter, there are elliptical holes or cutouts and holes of irregular shape caused by high-speed damage ...
Get Modeling the Effect of Damage in Composite Structures: Simplified Approaches now with the O’Reilly learning platform.
O’Reilly members experience books, live events, courses curated by job role, and more from O’Reilly and nearly 200 top publishers.