Chapter 4Delaminations
4.1 Introduction
Any separation between two adjacent plies in a lay-up is called a delamination (Figure 4.1). A delamination occurs any time an out-of-plane load causes local inter-laminar stresses that exceed the strength of the thin matrix layer between plies.
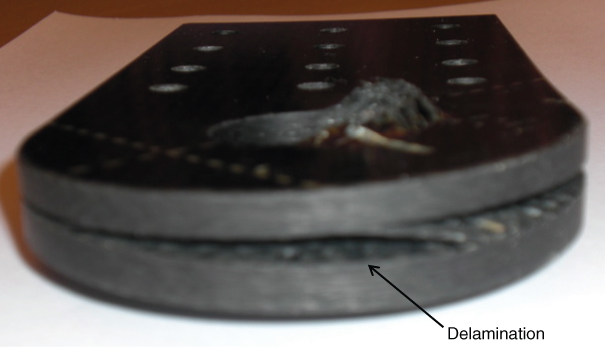
Figure 4.1 Delamination in a composite lug after transverse loading
The out-of-plane loads can be mechanical or hygrothermal. Mismatch in Poisson's ratios, coefficients of mutual influence (ratio of in-plane axial to out-of-plane shear strains) or swelling coefficients can cause local out-of-plane stresses. In addition, delaminations can occur as a result of other local failures such as matrix cracks. For example, matrix cracks in adjacent plies of different orientations may cause a delamination at the ply interface. This is shown schematically in Figure 4.2, where a 90° ply is shown above a 0° ply. Even though the static loading does not cause local damage which will lead to a delamination, it is likely that fatigue loading will.
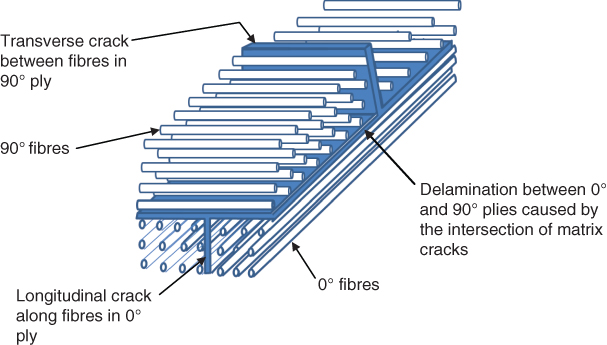
Figure 4.2 Intersecting matrix cracks causing a delamination at the ply interface
For some geometries such as the one shown in Figure 4.3, matrix cracks can evolve into delaminations under fatigue loads. Even low cyclic loads eventually crack the matrix in the ...
Get Modeling the Effect of Damage in Composite Structures: Simplified Approaches now with the O’Reilly learning platform.
O’Reilly members experience books, live events, courses curated by job role, and more from O’Reilly and nearly 200 top publishers.