Chapter 4. Materials
One of the most dynamic areas of development related to design is in material science. Design is visually enhanced by material selection. The allure of gold seems to be driven into our DNA while the textured grit of iron seems to suggest permanence. We love the changing patina of copper, the warmth of brass, the shine of aluminum and silver, the technical appeal of carbon fiber, the understated strength of titanium, and the invitation to touch by leather, wood, and texturized plastic.
Even though this is not a material science book, we have to give materials some mention because materials can save the day for a design in unexpected ways. I have had designs saved by such things as beryllium copper that will never spark, polyethylene that could be purchased in extremely long lengths, fluorinated greases that will not dissolve in fuel, and exotic coatings that provided high temperature service and wear resistance.
We have already considered material strength and stiffness, which include yield and ultimate strength as well as its response to stress (modulus of elasticity). However, there are many other important material attributes. For example, a material’s hardness is a characteristic that has practical importance in determining a part’s strength and wear characteristics. Hardness is defined as the resistance to penetration and is directly related to material strength. Metal hardness is usually changed by various heat-treating processes that modify the grain structure.
Other important material properties include density, dimensional stability, toughness, impact resistance, temperature weakening, water absorption, ultraviolet light resistance, flammability, thermal resistance, and a range of electrical, magnetic, and optical properties.
These are some common mechanical properties of materials:
- Density
- Hardness
-
Resistance to deformation. It relates to strength among other things; however, often surface hardness is made different than the material hardness through heat treating or other surface treatments.
- Impact resistance
- Modulus of elasticity (Young’s modulus)
-
Relationship between amount of stress and amount of stretch (stress/strain). This is the slope of the stress/strain curve.
- Toughness
-
Amount of energy a material can absorb before breaking. This is the area under the stress/strain curve.
- Ultimate strength
- Yield strength
These properties are most closely considered in plastics:
- Dimensional stability
-
Resistance to dimensional change due to temperature and humidity.
- Glass transition temperature
-
Temperature above which a hard material becomes soft. Note: metals have a ductile to brittle transition temperature.
- Water absorption
-
The rate at which water is taken into a material.
- Ultraviolet resistance
-
Resistance to degradation by ultraviolet radiation.
- Flammability
- Homogenous
-
A material that has the same elastic properties at all points.
- Isotropic
-
A material having the same elastic properties in all directions at any point in the material.
- Anisotropic
-
A material that is not isotropic with varying properties depending on direction.
- Orthotropic
-
A material that has three mutually perpendicular planes of elastic symmetry.
Note
While this list does not include electrical, magnetic, and optical properties, they are important too!
Selecting a material is a balance between performance, economy, and fabrication. But it is difficult to optimize on material selections. Sometimes favorites evolve based on experience and the following is an overview of some key materials—but remember the world of materials changes quickly! Where material properties are given, they provide a nominal value that is best used for comparison because material designations relate to chemistry and often do not provide the details related to such factors as mechanical properties, heat treatment, or quality.
Materials basically fall into one of the following categories:
-
Metals
-
Polymers
-
Elastomers
-
Ceramics
-
Glasses
-
Natural materials (such as wood and stone)
Characteristics of Metals
Strong, reliable, and the namesake for great Ages of history, metals produced the first industrial revolutions. Like wood, metals present appealing lusters ranging from the rich warmth of polished gold to the crusty slag of wrought iron that belies the maelstrom of fire from which it originated.
Steel
Steel is cheap and can generally give the highest strength-to-dollar ratio of any material. Beyond the pedestrian applications of steel, some alloys achieve exotic successes and can be sorted into the following categories: high strength, high toughness, high temperature, high hardness, and high corrosion resistance. Many nonferrous materials excel in these areas but usually at a higher cost, such as titanium for high temperature or gold for high corrosion resistance!
Carbon is the key element in determining steel characteristics. A small increase in carbon content greatly increases strength and hardness but reduces ductility. With low ductility, cold forming processes like stamping become more difficult. Cast iron is generally defined as “steel” containing more than 2% carbon. Cast iron is difficult to machine and bend, therefore shapes are normally produced by casting. The bulk of steel consumption falls in the range of low carbon steel. These steels contain less than 0.3% carbon and are interchangeably referred to as “low carbon” or “mild” steel. Steels with 0.3–0.6% are referred to as medium carbon steels and those with more than 0.6 percent are called high carbon steels.
Carbon content is so important in determining steel characteristics that it is embedded in the standard nomenclature for steel. For example, a popular cold-rolled steel is referred to as 1020. This number derives from SAE (Society of Automotive Engineers), AISI (American Iron and Steel Institute), and ASTM (American Society for Testing and Materials) designations. The “20” in these designations indicates the steel has a carbon content of 0.20%. Note the Unified Numbering System (UNS) is used in North America and includes a letter to indicate alloy type (e.g., C for copper, S for Stainless, and a five-digit number sequence); however, the four-digit and three-digit designations are very commonly used and will be presented here. For example, AISI 1018 is equivalent to UNS G10180. International equivalence can readily be found for UNS or SAE/AISI designations. It is important to note these material designations do not completely specify a material because they do not include material properties, heat treatment, or quality.
Many additives are routinely added to steel to ensure quality by reducing or sequestering impurities. For example, to remove crack-promoting sulfur, a small amount of manganese is added to combine with any residual sulfur. Silicon is also added to prevent oxygen from dissolving into the steel grains and making them brittle. Many other elements such as aluminum, cobalt, copper, lead, manganese, molybdenum, silicon, and tungsten are added to steel to develop specific properties. These steels are often referred to as “high alloy” steels. Tool steels are alloys of cobalt, molybdenum, tungsten, and vanadium specifically blended for cutting operations. Chromium alone or chromium and nickel produce alloys known as “stainless” steels. Using the four-digit system, the first number of some common steel alloys are 1 = carbon, 4 = molybdenum, 5 = chromium, 6 = chrome vanadium, 8 = nickel chromium molybdenum, and 9 = silicon manganese.
The second number in the designator indicates whether there are other significant alloying elements. So 1018 steel has no other alloying elements. Some other common alloys such as 1113 and 1141 have sulfur added to them to improve machinability. Letters are sometimes added in the middle of the designation such as B for boron or H for hardenability. For example, 11B41 is 1141 with boron added to increase the hardness. As mentioned before, the carbon content is given in the last two numbers; however, the actual carbon content can vary slightly from this percentage.
Common Steel Alloys
Common steel alloys include 1010, 1018, and 1020, which can be easily formed and welded. 4130 is commonly used in aircraft because it can be welded and hardened. 4140, 4340, and 6150 have high impact resistance and can be deep hardened.
Cold-formed steel, in which the steel is deformed at “cold” temperatures, creates a permanent increase in the hardness and strength of the steel. In order for these improvements to be sustained, the temperature must be below a certain range, because the structural changes are eliminated by higher temperatures.
Hot-rolled steel is heated and easier to form into a shape. Using the common three-letter designation (I know this gets confusing), we must comment on the ubiquitous ASTM A36 HR. It is cheap and strong but contains impurities, resulting in problems during machining. A36 has a yield strength of 36,000 psi (248 MPa), so it is a good material when your design will live a peaceful existence and is not subject to denting or other misuse.
Stainless Steel
Commercialized stainless steel developed quickly from research in the early 1900s. This early research was rooted in metallurgical studies of chromium in iron that went back as far as 1821. Stainless steels have provided the same reliable characteristics as steel without the problem of rapid corrosion. The term “stainless steel” was actually a trade name for the new chromium-nickel steel alloy. The easy-to-remember trade name has stuck. The austenitic stainless (300 series) steels contain chromium and nickel that combine to give the alloy excellent corrosion resistance. This type of stainless steel is very weakly attracted by magnets (referred to as paramagnetic)—notably different than the eagerly magnetized carbon steels.
The austenitic stainless steel cannot be heat treated, therefore it cannot be hardened like the other stainless steels. For example, low-chromium versions of ferritic stainless steels can be heat treated and are commonly used in cutlery. Many of the ferritic stainless steels are strongly attracted by magnets (referred to as ferromagnetic). This magnetic attraction challenges the time-honored method of differentiating stainless and carbon steels. Most stainless steel fasteners are made from austenitic stainless steel so the easily observed difference in magnetic attractions is usually an accurate method of differentiating between stainless and carbon steel. Stainless steels have a 30% higher thermal expansion coefficient and one-third the thermal conductivity of carbon steels.
Common commercial grades of stainless steel include the following SAE/AISI Types:
- 303
-
Contains 0.15% carbon, 17%–19% chromium, 8%–10% nickel, 2% manganese, and 0.15% sulfur. The sulfur is added to allow for easier machining. This grade is often used for fittings and other objects that require fine machining.
- 304
-
This alloy contains a maximum of 0.08% carbon, 18%–20% chromium, 8%–10% nickel, and 2% manganese.
- 316
-
Has higher corrosion resistance than 304, especially to acids. It contains a maximum of 0.08% carbon, 16%–18% chromium, 10%–14% nickel, 2% manganese, and 3% molybdenum.
Alloy modifications of these common stainless steels are often made and are noted by the addition of a letter. Most interesting are AISI 304L and AISI 316L. These steels have very low carbon content with a maximum of 0.03% and are used for high temperature applications.
Aluminum
Aluminum is a popular fabrication material, well known for its lightness and renowned for its ability to develop a highly polished luster. Like steel, there are numerous alloys of aluminum that are intended to produce a wide range of properties.
Alloys are designated by a variety of nomenclature; broad ranges of alloys can be summarized by the following series of numbers:
- 1000
-
Nearly pure aluminum, they are commonly used in electrical and chemical applications.
- 2000
-
Copper is the principal alloying element. Copper improves the strength of the alloy. However, it does not have good corrosion resistance and is subject to intergranular corrosion. 2024 is commonly used for aircraft components.
- 3000
-
Manganese is the principal alloying element. 3003 is a commonly used alloy because it combines strength, low cost, and formability. Formability is the ease in which a material can be bent, stamped, or otherwise deformed. The formability characteristic reflects a wide difference between the yield and ultimate strength.
- 4000
-
Silicon is the principal alloying element. The silicon lowers the melting point, so it is commonly used for welding wire. Some of these alloys can be treated so they turn a dark gray color. These alloys are popular for architectural applications.
- 5000
-
Magnesium is the principal alloying element. Magnesium is more effective than manganese in improving the alloy strength. These alloys have good resistance to corrosion.
- 6000
-
Magnesium and silicon are the principal alloying elements. This alloy combines the attractive characteristics of strength, corrosion resistance, and formability. This alloy can also be readily heat treated.
- 7000
-
Zinc is the principal alloying element. High strengths can be achieved with these alloys and they are used in the aviation industry for highly loaded components.
- Brass
-
Brass is corrosion resistant, and easy to mold and machine. Brass also has well-appreciated aesthetic attributes. Brass is an alloy of copper and zinc that offers an unusual set of qualities. Not only does this combination of elements increase strength, which typically occurs with an alloy, but it also increases the alloy’s ductility. Usually ductility decreases when a high-strength alloy is produced.
The major families of brasses are the copper-tin-zinc alloys, manganese-bronze alloys, leaded manganese-bronze alloys, and copper-zinc-silicon alloys (including silicon bronze).
Table 4-1 shows the composition of common brass alloys.
Alloy | Copper | Zinc | Tin | Lead |
---|---|---|---|---|
Gilding brass |
95 |
5 |
||
Commercial bronze |
90 |
10 |
||
Red brass |
85 |
15 |
||
Cartridge brass |
70 |
30 |
||
Yellow brass |
65 |
35 |
||
Free machining brass |
61 |
36 |
3 |
|
Naval brass |
60 |
39 |
1 |
|
a Percentage, actual composition, and trace elements vary. |
Bronze
Bronze was traditionally an alloy of copper and tin. However, the true definition of a bronze is an alloy of copper and any material besides zinc or nickel. The copper-tin alloys are very similar to brass. However, alloys of copper with aluminum, beryllium, and silicon produce some special characteristics. For example, aluminum bronzes can be heat treated to obtain relatively high strength. Copper beryllium is also heat treatable, very strong, resistant to sparking, and fatigue resistant.
The major families of bronzes are the copper-tin alloys (tin bronzes): copper-tin-lead alloys (leaded tin bronzes); copper-tin-nickel alloys (nickel is not a major alloying element); and copper-aluminum alloys (aluminum bronzes). Manganese bronze includes zinc as a major alloying element and therefore is a brass, not a true bronze. Copper-nickel alloys are actually a separate category of copper alloys that are very resistant to corrosion. Copper-nickel-zinc alloys (nickel silvers) fall into their own special category.
Table 4-2 shows typical compositions of bronze alloys.
Alloy | Copper | Tin | Zinc | Other major elements |
---|---|---|---|---|
Beryllium bronze |
98 |
2 Beryllium |
||
Silicon bronze |
96 |
4 Silicon |
||
Tin bronze |
88 |
10 |
2 |
|
a Percentage, actual composition, and trace elements vary. |
Nickel
Nickel is usually mixed with copper to make some remarkable alloys. They are usually difficult to machine but have remarkable corrosion and high-temperature characteristics. Monel is a common alloy comprised of two-thirds nickel and one-third copper.
Nickel is often the contributor to alloys with amazing characteristics ranging from the Nilvar alloy (nickel and iron) with its tiny 0.000001 in./in./°F (0.000002 mm/mm/°C) thermal expansion to the Inconels (nickel-chromium-iron) that have been used for such high-temperature, high-strength applications as the fuselage of the X15 airplane.
Magnesium
Magnesium is two-thirds the density of aluminum, which is its most significant advantage. It is used when weight is important but titanium is too expensive or difficult to process. Magnesium is often used in die casting to obtain exquisite details. Magnesium chips are very flammable and are used in fireworks and fire starters. Magnesium is often alloyed with other metals such as aluminum and zinc.
Titanium
Titanium has the best strength-to-weight ratio of any metal and is best known for its feats in aerospace applications. It is also corrosion resistant, especially to seawater and acids. Commercial alloys have yield strengths similar to the austenitic stainless steels. However, exotic alloys can have yield strengths of 200,000 psi (1,378 MPa).
Zinc
Zinc is commonly used for galvanizing, which is a thin, protective layer bonded to steel that provides corrosion resistance (see the section “Corrosion Behavior of Materials”). Zinc is also used to make high-definition die castings. Zinc has a low melting point of 787°F (419°C) and boils at 1665°F (907°C), so it cannot be welded at a high temperature such as produced with arc welding. Zinc is often alloyed with other metals in small quantities but processes such as casting or brazing may reduce the zinc concentration because of its low melting temperature.
Table 4-3 shows the mechanical strengths of common metal alloys.
Material | Typical alloy | Yield Strength, Tensile x 1,000 psi (MPa) | Ultimate Strength, Tensile x 1,000 psi (MPa) |
---|---|---|---|
Magnesium |
SAE AM265C |
11 (76) |
27 (186) |
Aluminum |
ANSI 3003-H14 |
21 (144) |
22 (152) |
Aluminum |
ANSI 6061-T6 |
40 (275) |
45 (310) |
Aluminum |
ANSI 7075-T6 |
73 (503) |
83 (572) |
Nickel-copper |
Monel 400 |
30 (207) |
79 (544) |
Titanium |
RS 140 |
140 (965) |
150 (1,033) |
Naval brass |
UNS C46200 |
53 (365) |
75 (517) |
Malleable iron |
SAE M3210 |
32 (220) |
50 (345) |
Steel |
ASTM A36 HR |
36 (248) |
58 (400) |
Steel |
AISI 1018 |
54 (370) |
64 (440) |
Steel |
AISI 1040 |
42 (289) |
76 (524) |
Steel |
AISI 304 |
35 (241) |
85 (586) |
Steel |
AISI 316 |
35 (241) |
85 (586) |
a Properties vary widely depending on processing and heat treatment. Properties for steels are based on hot rolling. Cold-drawn versions of the same grade are work hardened during the process and have higher strength values. The aluminum strength values are based on their specified temper. The naval brass strength value is based on hardened rod. |
Characteristics of Ceramics
Ceramics are derived from some of the earth’s most abundant minerals, including bauxite, clay, silica, feldspar, and talc. Ceramics cover a broad range of applications, from Chinese porcelain to heat shields on space craft. They are normally crystalline, hard, strong, brittle, and chemically impervious. Ceramics are well regarded for their excellent high-temperature performance—they can operate at temperatures up to 3,000°F (1,650°C). Their hardness allows them to be used effectively in cutting tools and abrasives. They enjoy an ancient history as pottery and construction materials.
Characteristics of Plastics
Plastics have revolutionized designs because of their remarkable ability to do wonderful things such as being slippery, strong, colorful, noncorrosive, and nonconducting. Currently, the main areas of weakness for plastics are with very low- or high-temperature applications and in applications requiring high surface hardness.
Plastics are usually based on long, repeating molecular arrangements called mers. This term is the root of polymers. Plastics have the same structure as all organic substances. They are composed of long chains of carbon atoms with hydrogen atoms branching off each carbon atom. Additional atoms are attached to these mers to give them their unique characteristics. For example, polyvinyl chloride (PVC) has a chloride atom attached to its mer. The molecular structure of organic molecules can be seen in everyday life. Their hydrocarbon structure can easily be altered by heat. When wood, bread, PVC pipe, or other organic structures are overheated, they become charred. That is, the hydrogen atoms linked to the outside of the hydrocarbon chain are driven free, leaving only the dark-colored carbon backbone.
The glass transition temperature of plastics is an important parameter for consideration. The glass transition temperature (or simply glass temperature) is the temperature below which the molecules cannot rearrange themselves when a load is applied. Therefore, at temperatures above the glass temperature, the plastic becomes rigid and brittle. Hard plastics, like the polystyrene used in plastic models, are used below this temperature while elastomers, like rubber, are used above this temperature.
Polymers have an inherent spring-like tendency because the bonds that hold the atoms together are at an angle. The amount of “springiness” is usually controlled by the amount of interconnection between the mers. As the mers become more interlocked, they transition from elastomers to thermoplastics and finally to thermosets.
Polymers can develop into a three-dimensional structure during initial fabrication. The three-dimensional structure makes the movement of molecules difficult when heated; therefore, once formed they do not soften at high temperatures. Consequently, they cannot be molded. This type of polymer is called a thermoset. Unlike thermosets, thermoplastic bonds disappear at high temperatures and thermoplastics soften at high temperatures. Therefore, these polymers can be easily molded and will only hold their shape when cooled.
Natural rubber, silicone, nitrile, fluoroelastomer, and other flexible materials are called elastomers. The glass transition temperature is especially important in elastomers because their desired quality of flexibility will completely disappear below that value. In fact, a rubber band that has been frozen in liquid nitrogen can easily be snapped like a piece of glass.
The main problem with most plastics is their poor performance at high temperature and their flammability and propensity to generate a lot of putrid smoke. Plastics are also prone to weakening from ultraviolet light, water absorption, dimensional instability, creep, and poor impact resistance
New versions of plastics are entering the market every day. The old standby “commodity” plastics (polyethylene, polypropylene, and polystyrene) and “engineering” plastics such as ABS (acrylonitrile butadiene styrene) and nylon have been tremendously enhanced over the years. Newer entries with complicated chemical designations and equally odd trade names have added even further to plastic’s market penetration. Many plastics can be modified to provide such enhancements as ultraviolet light resistance and internal lubrication. Moreover, the strength of almost any plastic can be increased by adding small, randomly oriented fiber reinforcements.
Table 4-4 shows the mechanical strengths of common plastics.
Material | Tensile yield strength: | x 1,000 psi | MPa |
---|---|---|---|
Polyethylene, high density |
4 |
27 |
|
ABS |
6.5 |
44 |
|
Polycarbonate |
9 |
62 |
|
Polyester |
10 |
69 |
Characteristics of Foams
Plastics are used to make foams such as Styrofoam. Foams are comprised of air with a thin matrix of solid material, typically urethane, polyester, and PVC. With all the air in the matrix, they are not very strong, but they are light and good insulators. Foams can be used alone for a variety of purposes, from thermal insulation to packing. They can also be used as the coring in sandwich construction.
Closed cell foams, as opposed to open cell, have sealed bubbles and therefore don’t absorb moisture. These are commonly used in exercise mats, sound absorption, and thermal insulators. Anti-static, conductive, and static foams are used for electronics packaging as well as sound proofing.
Some commodity foams include polyurethane, which is a cheap packing foam and has a tensile strength of less than 7.5 psi (52 kPa). High-density foam is used for furniture and has a tensile strength of less than 15 psi (104 kPa). Higher-grade foams are also used in furniture such as high-resilience foams. Viscoelastic (memory) foams are used in mattresses and medical supports.
Characteristics of Wood
Wood is a cellular material. Specialized cells provide structural support, and transmit sap or store food in the living tree. Wood cells are composed of cellulose, lignin, extractives, and ash-forming minerals. Wood is composed of 70% cellulose. Lignin acts as the adhesive matrix for wood. The ash-forming minerals constitute less than 1% of the wood and contain the stored nutrients for the tree. The extractives are not part of the wood structure but produce the characteristics of color, odor, and decay resistance. They include tannins, starch, oils, resins, fats, and waxes.
A cross-section of a tree shows two different colored regions. The lighter, outside ring is sapwood and the darker inside core is heartwood. Sapwood is usually less than two inches thick (5 cm). However, with ash, hickory, maple, and some pines the sapwood ring may be six inches (15 cm) thick. The sapwood consists of living cells that transport sap. The heartwood is older sapwood in which the cells have become inactive. The heartwood often contains minerals that give it a darker color. In addition, the heartwood of ash, hickory, and some oaks have much of their porosity plugged by naturally occurring ingrowths. The mineral content and plugged pores can give heartwood uniquely different characteristics compared to sapwood. White oak heartwood is used for liquid storage barrels because of its natural sealing. Another attractive characteristic of heartwoods is their resistance to organic attack.
Wood is anisotropic and the strength in the direction of the grain is approximately 10 times higher than in the direction parallel to the grain. That is, the grains can be pulled apart much easier than they can be broken along their length. This characteristic is accounted for by good design practice or by layering sheared plies at right angles as is done with plywood. Wood also warps readily outwardly from the tree’s core, as shown in Figure 4-1. Quarter-sawn lumber is the best cut because the grains run straight through the plank and will not warp.
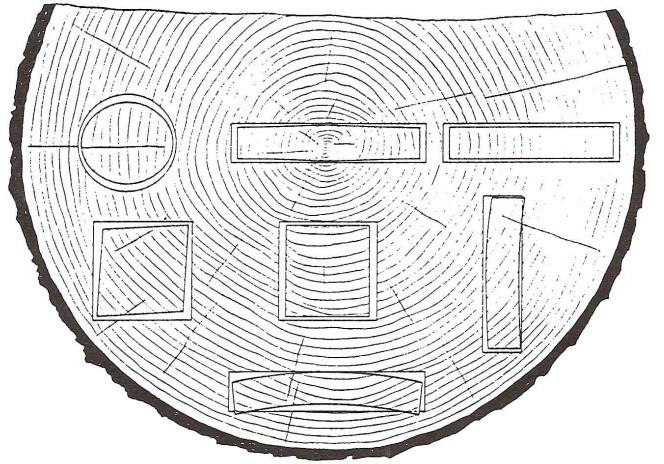
Figure 4-1. Wood warpage (image courtesy of USDA Forest Service, Forest Products Laboratory)
Determining the load-carrying ability of wood is based on many factors. Wood strength is decreased with the increasing presence of knots and other discontinuities (e.g., shakes, checks, and splits) as well as rot and moisture content. Again, the grain direction is the most important influence on strength. Laminated wood reduces the effect of knots by spacing them out across the wood and reducing the likelihood they will penetrate the entire laminate. The material properties of wood also vary based upon the type of wood and its moisture content. Oak is very strong in tension, and the tensile yield varies down through the hardwood and down into the softwoods such as pine and firs. White oak, for example, has twice the strength of Douglas fir in both shear and tension.
Wood is frequently glued to add tremendous strength to a screwed fastening. Glues or resins bond tenaciously to wood and distribute the joint loading over the entire joint rather than the area around the fasteners. Epoxy resins are excellent for bonding all types of wood, whereas polyester resin should not be used on redwood and close-grained woods such as oak or cedar.
Bamboo is a unique wood because its natural growth behavior produces a largely hollow structure. This makes it a natural tubing with a subsequently high strength-to-weight ratio.
Characteristics of Composite Materials
Composite materials are any substances made of two or more different materials. Natural materials are almost always composites, which are intricately mixed to make rocks, wood, soil, and nearly all other natural formations. Selecting complementary materials allows material scientists to customize composites for a particular application. Composites are typically understood to be a large-scale mixture of materials like the powerful combination of steel and concrete to make reinforced concrete. However, creative use of “composites” is also employed at the molecular level. Polymers and metals are often engineered with additives that add strength, ductility, and other desirable characteristics.
Composites used in fabrication generally consist of fibers and resins. The basic function of the fibers is to produce strength and stiffness while the function of the resin is to hold the fibers in place. In a more general form, fibers are referred to as reinforcements and resins as the matrix.
Composite materials, such as fiber-reinforced plastics (FRP), are stronger than the individual constituents because the resins are fluid and are able to transfer and distribute stresses among the fibers. FRP is a polymer-based matrix also known as a polymer matrix composite (PMC). There exist two other classes of composites based on the matrix material: the ceramic matrix composites (CMC) and metal matrix composites (MMC). Moldable plastics containing randomly oriented fiber reinforcements are also sometimes called “composites” although it is more common to refer to them as reinforced plastics.
Laminates, which are used to construct strong structural panels, consist of two or more layers of reinforcements, or plies, bonded by a resin. Sandwich construction is a special type of laminate construction that increases the rigidity and buckling resistance of the laminates by increasing the moment of inertia. By placing a thick but light and relatively weak core between two strong laminates, the assembly becomes much more rigid than if the two laminates were simply bonded to each other. The increase in rigidity is produced by the greatly increased moment of inertia resulting from the thickness.
Recall that for a given load, the deflection decreases with increased moment of inertia. Doubling the thickness increases the moment of inertia by eight (I = bh3/12 for rectangular cross sections). The stresses in the core remain low under flexural loading because they are close to the neutral axis, therefore the c term in the flexural stress term is small (σ = Mc/I). Thus, making something thick makes it really strong and rigid and you can put cheap, weak material in the middle and it won’t matter.
Commercial cores sold under various trade names include end-grain balsa wood, urethane foam, PVC foam, Kevlar honeycomb, and aluminum honeycomb.
Characteristics of Fibers
Fiber material is the principal indicator of a composite’s strength. This is why we refer to the composite by its fiber material. Fiber strengths are so high they are waiting for the resins and designs to catch up to their ability. The principal fiber materials for FRP construction are fiberglass, aramid (e.g., Kevlar), and carbon. These materials are sometimes mixed to provide a balance of strength and economy. Let’s briefly review each of them:
- Fiberglass
-
The fiberglass fiber varieties referred to as E-glass and S-glass are the most common structural fibers. E-glass is an alumino borosilicate glass and is the most commonly used glass in fiberglass-reinforced plastic. S-glass is about 33% stronger and 25% stiffer than E-glass but is also more expensive. Both fibers are white when dry and translucent when wetted with resin.
- Aramid
-
Aramid (e.g., Kevlar) fiber was one of the first so-called “advanced” composites and is much stronger and stiffer than fiberglass. Aramid fibers derived from nylon are well known for their impact resistance. They are also excellent energy absorbers and fail in a ductile manner unlike the brittle, glass-like failures that occur in fiberglass and carbon.
- Carbon
-
Carbon fiber is also considered an advanced composite, and due to its strong molecular bonding, is very solid and rigid. Stacks of hexagonal carbon plates are attached at the ends to form filaments. These tightly bound carbon plates make the filament strong. However, this same characteristic also produces a slippery surface and makes resin bonding difficult.
The mechanical properties of carbon are highly dependent on the nature of the parent material or precursor. As a result of this dependency on a specific precursor, there are a variety of carbon-fiber composites, each with differences in strength and stiffness. Current carbon-epoxy composites can achieve tensile yield strengths of 160,000 psi (1,100 MPa). Carbon has some other impressive features—for example, its strength increases with temperature and it has low thermal expansion.
One of the problems with carbon fiber is that its highly cathodic electrical nature can produce strong galvanic corrosion. Consequently, when metal fasteners are required, they must be made from stainless steels, inconels, or titanium.
Characteristics of Adhesives
Most adhesives create a mechanical lock between surfaces. The adhesive works its way into the nooks and crannies of a surface and then hardens, creating a locking matrix. The adhesive is further connected by molecular surface forces (hydrogen bonding or Van der Waals’ interaction) or shared electrons (covalent bonding).
Adhesives fall into one of these categories: wet, contact, or reaction. Wet adhesives, such as polyvinyl acetate (PVA or white glue), usually have a solvent that evaporates and creates intimate contact between two materials. These are best for porous materials. Contact adhesives are applied to all the materials being bonded. After an evaporation time, they can be united and will immediately bond. Reaction adhesives are usually two-part adhesives where one part is a catalyst that rapidly causes the adhesive to cure. Single-component versions may be triggered by such things as ultraviolet light.
Cyanoacrylate adhesives (CA), such as superglue, come in different thicknesses. They form a strong mechanical bond when the water present on the surface combines with groups of cyanoacrylates to rapidly harden. Van der Waal forces lock the bond. CA accelerants allow faster cure and the ability to adhere things with CA that might not normally adhere. CA accelerants are helpful when bonding wood structures such as balsa or basswood, but the smell can be especially bothersome. CA is brittle with low-impact resistance, but the instant connections are great for wooden model making.
The strongest bonds are made with polyurethane and epoxies. Polyurethanes produce mechanical bonds but also link to materials, such as the cellulose in wood, with powerful covalent bonds. Epoxies are two-part systems that become very strong and can be used to fill gaps. They can be mixed with fillers to make a putty or obtained in optically clear forms, which is helpful if you want to show off underlying materials. Epoxies are the strongest bonding agent for high-performance fibers such as carbon.
Polyvinyl acetate (PVA), such as craft glue, works in the same way but the connection to the materials is through weaker hydrogen bonds. Polyvinyl acetate is water based and relies on evaporation, and is therefore slow to cure. However, it is easy to clean up, has low toxicity, and is initially tacky so it can be more comfortable to work with. In addition, you can fill it with sawdust to make a cheap, sandable joint filler. PVA is also used as a fabric adhesive, which is great for prototyping soft goods, especially if you have poor sewing skills.
Hot glue is a simple and fast glue in which a polymer glue stick is heated and extruded onto a surface. It cools quickly and produces a mechanical bond between anything. This hot melt adhesive (HMA) technique is great for prototyping—it gives an ugly joint but you can count on it. However, the commonly used low temperature version is not very strong or temperature resistant. It is good to have a wet towel nearby to cool the inevitably burnt fingers.
Pressure -sensitive adhesives (PSA) and spray adhesives produce instant surface adhesion and are helpful for adhering graphics and surface veneers.
PVC cement is comprised of materials that dissolve PVC, especially tetrahydrofuran. Once the PVC is softened, cross-links are formed between the mating PVC materials. The solvents used to clean the PVC consist of tetrahydrofuran plus powerful cleaning solvents such as acetone and methyl ethyl ketones. PVC is a fast material for making large structural models, compressed air cannons, and even water lines.
Some specialty adhesives that are helpful for designers are fabric adhesives that can replace sewing and are especially helpful for building fabric models. Other specialty adhesives include thread locking adhesives, which are anaerobic and are designed specifically for fasteners.
Composite structures are made using adhesives, such as epoxy, urethane, or methacrylate. Methacrylate will work through oil films so less surface preparation is required. The layering of fiberglass and epoxy over a wood structure can give it new life, and is helpful for building high-strength, weather-resistant wonders. Figure 4-2 shows my new wooden boat covered with fiberglass and epoxy.
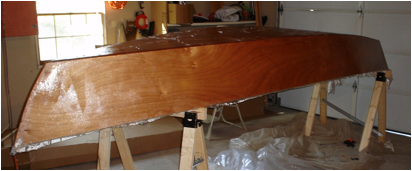
Figure 4-2. Wooden boat covered with fiberglass and epoxy
Corrosion Behavior of Materials
Corrosion ranks with fatigue as the most common causes of material failure. However, corrosion and fatigue usually work together: what corrosion starts is often finished by fatigue. Fortunately, the advent of plastics, stainless steels, and nickel alloys has provided great immunity from the continual corrosion process.
In 1780, the Italian anatomist Luigi Galvani hung some recently killed frogs from copper hooks. To his surprise, the frog’s legs started kicking! As it happens, the copper hooks were connected to an iron rod. Fortunately, Galvani knew an electrical current would produce the same reflex action in the frog legs. Therefore, he connected the reflex action of frog legs with the unintentional and macabre phenomenon he observed on the copper hooks. This “animal” current, as it was originally called, led to experimental investigations into the remarkable phenomenon of galvanic corrosion and our current understanding of corrosion.
Because corrosion is a chemical process, it involves intricate discussion of electron behavior. However, there is a range of corrosion behavior from materials that never corrode, such as plastic and nickel alloys, to those that corrode with alacrity, such as steel. Between these extremes are metals that usually do not corrode but can do so under special circumstances, such as aluminum and stainless steels. The special circumstances are usually the wrong mix of metals, or exposure to acids and saltwater. Designers either need to avoid these situations or select the right material to accommodate them.
Anodes and Cathodes
Corrosion results from two materials exchanging electrons. Metals have loosely attached electrons and will readily give them up to other materials. The material that gives up electrons, and consequently loses material, is called the anode, while the material that receives the electrons is called the cathode. The propensity of a material to give or receive electrons from another material is determined by the electrochemical nature of the material. The flow of electrons produces an electrical current and the use of anodes and cathodes is used to great advantage in batteries.
However, designers should avoid the corrosive reaction of metals by considering their galvanic relationship. This is important when the metals may become wet or are used in a humid environment. Metals that have similar electrochemical behavior generally will not cause each other to corrode. Some materials, such as aluminum and copper (including its alloys of brass) will cause corrosion if they are in intimate contact. Galvanic corrosion is eliminated if they are separated by a nonconducting material or if they are kept very dry.
Rust
Rust is caused by the iron in steel reacting with the oxygen. Oxygen is present in both air and water. The iron and oxygen molecules combine to form the nonwater soluble rust. The reaction sequence is described here:
-
Fe → Fe3+ + 3e - (An iron atom dissolves, creating an iron ion and three free electrons. This reaction actually occurs in two steps.)
-
4e - + 2 H2O + O2 → 4(OH)- (Four free electrons coming from the iron reactions, two water molecules and one oxygen molecule react to form four hydroxyl ions.)
-
Fe3+ + 3(OH)- → Fe(OH)3 (The iron ion reacts with three hydroxyl ions to form one insoluble rust molecule.)
Oxygen forces nearby metals (which readily shed electrons) to become anodic. Zinc and magnesium have a higher electrode potential (a relative measure of their naturally occurring voltage with respect to hydrogen), and therefore protect steel. Zinc and magnesium offer this protection because they readily donate electrons, with greater propensity than does the iron in steel. Because of their very loosely held electrons, zinc and magnesium are often used as sacrificial anodes in hot water heaters and boats. They corrode away instead of the steel tank or hull. These materials become unwitting accomplices in a designer’s plan for corrosion protection.
The following zinc and magnesium reactions occur faster than the dissolving of iron that was previously discussed:
-
Zn → Zn2+ + 2e - (A zinc atom dissolves, creating a zinc ion and two free electrons.)
-
Mg → Mg2+ + 2e - (A magnesium atom dissolves, creating a magnesium ion and two free electrons.)
The electrons contributed by the zinc or magnesium then react with the hydroxyl ions produced by the solution of oxygen.
Some metals, including stainless steel, aluminum, and titanium, can be passivated by isolating the metal from the cathode. In stainless steels, the chromium is strongly attracted to oxygen and forms a protective oxide layer. In a similar manner, aluminum and titanium both react with oxygen to form a thin, protective oxide layer. This passivation reduces the rate of corrosion but does not eliminate it. The coatings are susceptible to chemicals that will strip the oxygen away and destroy the oxide coatings.
The following list includes common materials and their relative galvanic relationships in seawater. The further apart the metals are in the list, the greater the galvanic action and subsequent corrosion. For example, graphite is used with zinc in dry-cell batteries. The list shows some metals in their position when passivated. The loss of the passivation will make them much more anodic. This listing presents an average for alloy’s galvanic relationship and subtleties exist among specific alloys, such as stainless steel:
Most anodic
-
Magnesium alloys
-
Zinc
-
Aluminum alloys
-
Carbon steel
-
Cast iron
-
Tin
-
Brasses
-
Copper
-
Nickel-copper alloys
-
Titanium
-
Platinum
-
Graphite
Most cathodic
This list illustrates some of the following points:
-
Brass and steel hardware should not be mixed.
-
Aluminum will slowly corrode around steel fasteners and quickly corrode around brass fasteners.
-
Zinc and magnesium can be used to protect steel, brass, and almost any other material.
-
Graphite is more cathodic than any other material it contacts.
Electrolyte conductivity accelerates galvanic action. Therefore, galvanic corrosion increases with increasing temperature, salinity, and pollution. The edges of bolt threads expose a lot of surface area and will quickly show galvanic corrosion.
Crevice Corrosion and Pitting
Small crevices and cracks between materials can restrict the free movement of an electrolyte and lead to an electrolyte that has a different composition in the far reaches of the crack. This system is called a concentration cell. Many different types of concentration cells exist depending on the composition of the materials. However, the oxidation-type concentration cell is one of the most common and is a typical cause of crevice corrosion.
Concentration cells are an important phenomenon because they produce corrosion in difficult to view areas such as underneath fasteners, clamped joints, scale, dirt, and cracks. Moreover, this accelerated corrosion in stagnant crevices can eat deeply into a small area of the material and make it weaker than the surface condition indicates. Crevice corrosion is a bigger concern with metals that rely on passivated (oxide) coatings for protection, such as stainless steel and aluminum.
Like crevice corrosion, pitting can deceptively weaken a material. Pitting is initiated without a crevice and occurs randomly over the surface of a metal. Pitting becomes more prominent than overall surface corrosion in metals that either have high alloy content or develop protective oxide coatings.
Intergranular Corrosion
Many alloys are also subject to intergranular corrosion. This corrosion shows as a web of cracks, typically made more obvious by the corrosion in the cracks. The composition of the grain boundaries may be different from the grain, resulting in a lack of protection for the material at the grain boundaries.
Microscopic galvanic corrosion can actually occur within an alloy where two different grain compositions are present such as in aluminum alloys. Corrosion can also be initiated by stress cells in which the stressed part of a material acts as the anode and the unstressed part acts as the cathode. This can be seen in metals formed by such processes as bending or stamping.
Stress Corrosion Cracking
Stress corrosion cracking is caused by a combination of tensile stress and intergranular corrosion. The material stress may be produced either externally or by residual stress produced during manufacturing (e.g., punching). Stress corrosion cracking creates the dangerously surprising condition in which a normally ductile material fails in a brittle manner.
Corrosion Characteristics
The following list summarizes the most common forms of corrosion in various metals:
- Steel
-
Unpainted or uncoated carbon steel will rapidly rust, especially when subjected to salt or other electrolytes. The rust is coarse textured and flaky. Polished and hardened steels corrode more slowly than unfinished steels. Many paints and coatings now permit steel to be used successfully in outdoor applications.
- Stainless steel
-
Stainless steel is well known as being resistant to corrosion. While an oxide layer protects the metal, it is vulnerable to pitting and crevice corrosion. Stainless steels with a low chromium and low nickel content are the most susceptible to corrosion.
- Cast iron
-
Cast iron will rapidly form a rust surface that bonds to the underlying iron. The bonded rust does not instantly flake off (as occurs with steel) and protects the iron from corrosion. The bonded rust is brown colored but can look almost black when submerged in water. Nickel and silicon cast irons have the best corrosion resistance, however all irons have very good resistance.
- Aluminum
-
Aluminum is very corrosion resistant because of its strongly bonded oxide layer; however, it can be subject to both pitting and crevice corrosion. Aluminum is also very vulnerable to galvanic corrosion because it is very anodic. Therefore, it must not be in direct contact with more cathodic metals, especially copper alloys. This is especially a problem when an electrolyte is present. In dry environments galvanic corrosion between aluminum and other metals is uncommon. Corroding aluminum often produces a crusty, light-gray scale.
- Copper alloys
-
Brass and bronze will readily corrode when in an electrolyte (like seawater) and in contact with steel or aluminum. Corrosion can appear in different forms from a rough green to a smooth brown appearance. Brass and bronze are also susceptible to the weakening effect of dezincification, which is the leaching of zinc from a material. Dezincification can produce a bright copper color. Brass will also react with ammonia, a common component in cleansers, producing a blue-green corrosion.
- Nickel alloys
-
Nickel alloys are virtually impervious to corrosion. However, pitting is possible with some alloys.
Closing Thoughts
You know materials are the raw ingredients for your design. Their capabilities inform how you design something. If you want something light and strong, you know that a carbon-fiber composite or aluminum are the best choices. You know they need to be processed differently and can be expensive. If it weren’t for money, you’d probably design everything to be made out of titanium! You know if you need something to be cheap, you will consider the commodity plastics like polyethylene. Maybe you will consider cardboard or cast iron.
You know that materials are evolving, so “cheap” plastic has moved to high-temperature, high-strength, UV-resistant super material. You can even make them conductive with a range of textures, colors, and other appealing properties. However, you know there is an aesthetic appeal to wood, stone, and metals that is vital in some designs.
Materials can cause us grief. They can be beautiful to look at and touch, but they can be difficult to process or repair. They can have incredible strength, but be extraordinarily expensive. With so many material choices, you will probably end up with your favorites—a palette of materials that are almost perfect for every design.
Get Engineering for Industrial Designers and Inventors now with the O’Reilly learning platform.
O’Reilly members experience books, live events, courses curated by job role, and more from O’Reilly and nearly 200 top publishers.